电液锤
参展单位:德国拉斯科成形技术有限公司(LASCO)
展品型号和名称:GH 4000对击式电液模锻锤
技术参数
打击能量400 KJ
总行程770 mm
上锤头行程585 mm
下锤头行程185 mm
模具最小闭合高度(不含燕尾高度)530 mm
模具最大闭合高度(不含燕尾高度)1000 mm
导轨间距1285 mm
锤头深度1600 mm
上锤头重量27,000 Kg
下锤头重量98,000 Kg
GH 4000对击式电液模锻锤是目前国内外已投产使用的最大规格的对击式电液模锻锤,已在国内外投产使用数台,其中一台于2012年安装在张家口煤矿机械公司锻造分公司。
与气锤相比能量消耗较低。
上撞锤与下撞锤的质量比为1:4。
不同的撞锤速度,防止自由锻造形成跳跃。
高打击频率。
不同模具高度拥有持续打击能量。
小型液压系统分路阀箱,无需液压管。
依靠严格可重复能量利用和较长模具使用寿命(短加压时间)节约能源。
通过锤头控制拟定锻造程序。
低撞锤的稳定起始位置便于处理或自动操作。
在偏心锻造情况下,弹性锻造活塞杆的使用寿命长。
通过热中立导向系统,保证精确的导承间隙。
大范围的模具高度可使用各种各样的模具。
专用安全节气门带有下活塞杆导向。
参展单位:德国拉斯科成形技术有限公司(LASCO)
展品型号和名称:HO-U 1250全液压电液模锻锤
技术参数
打击能量125 KJ
最大打击能量下,打击频次75 1/min
锤头最大行程1000 mm
锤头最小行程750 mm
锤头深度1000 mm
锤头重量8,500 kg
两个立柱的开档1000 mm
是目前国内外“U”机架中最大规格的电液模锻锤,已在国内外投产使用数台,其中中国有两台,一台于2000年安装在沈飞集团锻造分公司、一台于2012年安装在张家口煤矿机械公司锻造分公司。
高框架重量(168吨)和锤头重量(213吨),质量比为撞锤:框架=8500:168000,近似为1:20。因此,将随弹簧阻尼进行低振幅上下运动。由于撞锤和框架之间的高质量比,模锻锤的冲击效率也相应增加。
框架拥有大底座(4100 x 3100毫米),便于在下方安装所有必要的弹簧阻尼组件。
铸造油箱(无焊接结构)。我们的油箱设计为铸造结构,可以获得高延展性,从而吸收每次冲击产生的强压。
大范围的模具高度可使用各种各样的模具。
锤头真正的减速功能可用于工具更换及维护。
专用安全节气门带有下活塞杆导向。
设置为10–100 %之间的冲击能量可以将冲击能量的精确度控制在± 1%。
由单片铸造而成的光滑活塞杆可以带来良好的耐用性。
电力传动能力为2 x 132千瓦可以产生大量可用冲击,提高生产力。
通过分离的外壳,极为安全地将蓄能器气囊固定在贮油槽中。
参展单位:江苏百协精锻机床有限公司
展位号:W2-R27
展品型号和名称:CTKA250KJ数控全液压模锻锤
技术参数
打击能量:250KJ
打击行程:1100mm
打击频率:50次/分
百协CTKA250数控全液压模锻锤采用高度集成的液压系统和锥阀式控制,复合缸结构,高低压双重防外泄技术及双阀联动控制技术,实现了设备的高效、节能、高可靠的全液压动力驱动;采用了在线传感、数字显示、自动监测控制技术,实现了打击能量、打击步序的自动控制;采用可方便调整间隙的放射状X形宽导轨结构和组合式砧座结构,实现打击系统的高精度可靠运行;采用国际先进的液压阻尼+弹簧隔振技术,有效控制了振动对周围设备的影响;采用液压动力泵站系统与全液压驱动系统分离式近距离安装结构,缩短了管路,避免了锻锤打击振动对液压系统的影响。采用高压软管油箱内隐藏安装结构,避免了高压软管爆裂引起高压油喷射的安全隐患。
热模锻压力机
参展单位:江苏扬力集团
展位号:W1-G58
展品型号和名称:HFP25型2500吨热模锻压力机
技术参数
公称压力:25000kN滑块行程:320mm锻造工作节拍:12-15spm
最大封闭高度:1000mm下垫板尺寸:1500*1700(左右*前后)
上垫板尺寸:1500*1320(左右*前后)
1.创新技术介绍
1)宽台面、高抗偏载能力的曲柄—滑块机构。
利用加宽支撑的偏心轴、高强度横向布置的偏心柱销、以及加宽设计的滑块,可有效提高设备的抗偏载能力,并可适应第三代轮毂轴承单元锻造需要的5工位布置的要求
2)高稳定性的、齿圈导向的新型离合器、制动器。
在现有的德国技术基础,并结合扬力集团多年来离合器、制动器的设计制造经验,将普通的柱销导向的闸块式离合器制动器,改制成内外齿圈导向的新型离合器制动器,运动部件的运动平稳性更高,且结合面的贴合度与同步度更好,摩擦块的摩擦状况和受力平稳性更佳,可有效的提高压力机核心部件的可靠性,延长设备维修或保养周期,提升设备品质。
3)高协调性的机械式上下定出系统。
经过优化凸轮曲线,并结合实际锻造工艺需求,对特定锻造条件下的顶出系统进行优化设计,其中,下顶出系统在最高顶出位置柔性机械性接触先顶动工件,再利用平稳的气动顶出系统进行二次顶出,且能保持在一个稳定高度上直至设定时间,有利于工件的稳定顶出和机械式加持工件,操作方便可靠;上顶出系统的顶杆,与滑块运动曲线严格匹配,实现上顶杆下行顶出与滑块回程速度高度一致,从而实现工件顺利脱出上模而不被带出模腔。
4)任意角度可调的封闭高度调节系统。
常规的热模锻压力机一般只能在上死点进行封闭高度调节,本项目通过巧妙的去除平衡缸施加在压紧杆上抱紧偏心销的固锁力,并确保滑块不因为平衡缸的平衡力消除造成的轻微下沉,可在任意角度进行封高调节,且封闭高度调节精度更高。
2.使用新技术介绍
1)采用高性能可编程控制器+增强型高性能变频器系统。
本项目采用日本三菱公司高功能处理器做为主控制器,增强型高性能FR系列重型变频器驱动压力机主电机。该控制器具有双核处理器,可极快的进行数据处理,且CC-link网络具有极可靠的冗余安全技术。FR系列重型变频器功能强大,具有易于使用、灵活、节能且适用于各种工业应用的特点。具有嵌入式控制技术,支持离散输出处理和变频器控制功能。
2)拥有全自动快速换模中心。
全自动快速换模中心具有移动台车、自动模架更换装置、左右备用模架库、全自动换模升级平台、自动伸缩升降关节换模臂等,可有效减少模具和模架更换时间,提高锻造生产率。
3.攻克难关介绍
本新产品研制的目的是:利用自动化技术与热模锻压力机技术结合起来,开发出一种热模锻自动生产线,以此来与国际上大的企业在争夺高档次的市场份额,来提高公司的技术力量和经济效益水平。通过研发过程中新技术、创新技术的使用,使机床具有自动化程度高、生产效率高、用人少;结构紧凑,占地面积少;操作安全,可靠;工件锻造周期和流程短,锻件精度高;节能节材,综合成本低;并可配备其他辅机,完成复杂锻件的自动化锻造成形的特点。
参展单位:俄罗斯伏龙涅什重型机械压力机股份公司
展位号:W2-W87
展品型号和名称:14000吨曲柄热模锻压力机
技术参数
额定压力:14000吨,滑块行程:520±1.0
用于对卡车上曲轴和前梁锻件(先前经过加热。辊轧的毛坯)进行三工位热模锻加工。压力机机架由两个带有导轨的立柱、横梁、前撑板、后过梁和带有职称底角的工作台所组成。压力机的立柱、横梁和工作台通过四根拉杆互相固定在一起。压力机的前面和左侧导轨是可以调节的。皮带轮、三角皮带、飞轮和离合器的旋转部件金属防护罩保护。
参展单位:株式会社栗本铁工所
展位号:W2-W76
展品型号和名称:C2F-40GWL宽台面双模压力机
技术参数
能力40mn・装模高度1450mm・行程长度550mm
行程数量40rpm・滑块调整量10mm・上垫板尺寸1900mm×1760mm
下垫板尺寸2200mm×1810mm・压力机高度9000mm
设备特点
・长行程,宽台面的大吨位自动线,适用于CVT等轴形件生产
・实现高速锻造,保证模具寿命前提下,自动化稳定性高。
・一台设备上可实现上死点停止与上死点不停止两种模式互换。
・全电气控制,可针对锻件特性进行锻造条件微调。
・2段轴机构。蓄能快,设备体积小。
润滑液,氧化皮回收装置,实现环保。
参展单位:住友重機械工業株式会社
展位号:W2-W41
展品型号和名称:住友自動化鍛造圧力機(TFPX系統)
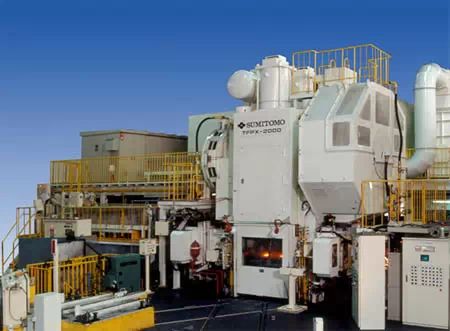
(1)利用有限元设计解析(FEM)达到高钢性、高可靠性主机框架的目的
a.为达到锻件高精度化、要求设备具备高钢性和高強度的主机框架。
本压力机的主机框架为3体构造、上横梁以及机座的高负荷受重部位采用铸钢,左右立柱采用钢板焊接,用高强度拉紧螺栓连接,使机身具备压紧应力的构造。
b.主要零部件进行超音波探伤、磁粉探伤、着色探伤等检测,严密执行品质检查工序。
c.依据FEM进行刚性計算、使用油圧式千斤顶进行负载实测各部位的应力,完全的性能测试,高性能的主机架体的设计。
(2)为使锻件实现高精度化而提高设备性能。
a.解决偏心负荷的影响、采用超宽的双支点式连杆,滑块采用长导轨结构,采用合金铸钢件。
b.为保证滑块导向板的间隙要达到最小、使滑块导向板受热膨胀影响减少,设计时采用了“X”型构造。同时采用模架的“X”型 导柱方式(住友专利)减少模具的偏离现象。
c.闭合高度的调整利用微调导向板上设计的偏心轴编码器方式、可以快速进行调整。調整量显示在操作盘上的触摸荧屏上。
d.为提高锻件厚度精度(下記①~③为住友专利)以及解决超负荷现象、设备还附加设计了以下功能。
①有步进梁急停时,防齿错位功能。
②有锻件锻打开始和锻打动作结束前、根据模具上的锻件个数进行闭合高度的自动調整功能。
③设备正常运行时、模具,机架等部件因温度上升影响锻件厚度时,利用锻造负荷的数据反馈控制系统来解决不良产品影响。
(3)提高耐久性
a.离合器,刹车系统为散热性强,寿命高、且维护性能也非常优秀。
采用了可拆卸式摩擦板(马蹄形)。
b.下工作台上面、滑块下面的中间垫板采用S45C。
c.各种OST配管、模具润滑用配管及冷却水配管使用防腐蚀性能高的SUS材。
(4)使用高速稳定的三维步进梁传送机构
a.住友独特的交流司服马达控制三维步进梁转送装置、10轴驱动,简洁、精巧的构造,在高速运行中能够稳定运送。
b.前后传送梁及夹钳可单独控制,搬送更准确,降低故障率。
C.材料进、出部不安置机器设备,作业空间宽敞,维修、维护方便。
(5)自动喷射模具润滑装置
a.实现高速自动化鍛造的关键在最佳的模具润滑装置。为达到模具内部充分润滑、模具冷却效果追加、压力机后面设置了式伺服电机驱动式自动喷淋机械手,且喷嘴部采用了住友独创的增压系统,并达到高速锻造情况下充分的润滑功能。
(6)快速自动换模装置
a.压力机前面有T型模具自动交换台车、上下模具和模架整套可同时进行交换、减少压力机的停顿时间,十分钟内完成模具交换。
B.步进梁装置的夹送臂中央部分与驱动臂采用自动分离装置、和模架一起进行。
(7)作业环境的改善及安全
a.曲轴与连杆的轴承、滑块导轨上镶嵌的衬板、采用循环式稀油润滑方式、使工作环境大大改善。
b.具有超負荷检测、润滑異常检测等的各种检测功能,确保设备的安全使用。
c.锻造部位有安全防护门及锻机上部分有安全围栏,以及安全保护连锁等安全装置,体现了对工作者的安全防护。
D.运行数据设定、荧屏異常显示功能使用触摸荧屏、提高了设备操作性。
电动螺旋压力机
参展单位:武汉新威奇科技有限公司
展位号:W2-W18
展品型号和名称:J58K-400数控电动螺旋压力机
技术参数
公称压力(KN):4000
长期运行许用载荷(KN):6300
运动能量(KJ):40
滑块行程(mm):400
行程次数(次/分):24
最小封闭高度(mm):570
工作台尺寸(左右×前后):750×730
1.J58K系列数控电动螺旋压力机整体设计方案新颖、合理,具有结构紧凑、运动控制精度、运行效率和工作可靠性高、电网冲击小、节能降耗等特点,满足了不同用户的加工工艺要求。
2.研发了一种多变频电机带动齿轮同步直接传动的新型结构,简化了传动系统,提高了传动效率;开发的高分子材料小齿轮通过碟簧与电机轴连接为一体,缩短了传动链,减小了转动惯量,降低了运行噪声;基于直接转矩控制技术(DTC)的交流异步电机驱动方式和编码器同步技术,实现了打击能量的精确控制,提高了锻件精度和模具寿命;对电机的轴系结构、机壳和散热构件进行改进和优化,提高了电机的抗冲击和散热性能。
3.该项目系列产品实现了规模化生产,并成功应用于工程实际,在国内多个行业建成了一批由项目产品数控电动螺旋压力机为核心设备的全自动化精密模锻生产线,取得了显著地经济效益和社会效益。
参展单位:意大利菲赛普(FICEP)公司
展位号:W2-V33
展品型号和名称:DD系列电动直驱式螺旋压力机
技术参数
550 -6400吨
菲赛普公司创造性地将旋转直线马达应用到螺旋压力机上。马达永久磁铁直接固定在压机飞轮(同时也是马达转子)上,而马达定子固定在机架上。这一方案,除了从制造角度看非常简便之外,还使得击打过程产生的系统振动及强烈减速过程对马达–飞轮机组本身的有害影响极度降低。此外,直线马达所特有的高效及动态特性可获得下列显著效果:
较高的击打速度,减少了模具损耗
可获得更高的能量,即使在滑块的3/4行程,也能获得高能量
明显减少循环时间,提高生产效率
可以精确编制和重复所需能量,在单冲程或多冲程工况下按要求取得不同能量值
大大减少维护时间,节省维修费用
极高的工作效率,节电达50%以上
参展单位:淄博桑德机械设备有限公司
展位号:W2-T23
展品型号和名称:SD20系列电动螺旋压力机全自动锻造成型生产线
技术参数
型号SD20-400
公称压力4000
最大压力8000
滑块行程500
行程次数22
装模高度700
工作台尺寸左右前后厚(mm)1000/950/120
整机尺寸(mm)
高5010
宽3560
厚2060
总重量28
电机功率55
经过俩年多的努力开发成功电动螺旋压力机全自动锻造成型生产线,并且获得国家专利授权。
电动螺旋压力机全自动锻造成型生产线:人工下料到料筐→人工转料到中频加热炉的自动上料斗内→中频炉加热(带材料温度分选和炉料清空棒)→步进梁将加热好的棒料放入压力机的制坯台上→制坯→成型→冲孔(切边)→出料;在成型工位移动同时进行自动喷墨,对成型模具进行上下自动喷墨。
攻克难关:利用宽台面的压力机布置步进梁,设计自动扶料装置,将中频加热后的合格棒料放入步进梁工位内,利用伺服电机控制步进梁XY三轴联动,完成棒料、坯料、成型、冲孔(切边)工件的直线位移。整个成型不需人工介入。步进梁分为双臂步进梁和单臂步进梁,双臂步进梁电动螺旋压力机自动生产线适合于大件及复杂件的成型。单臂步进梁电动螺旋压力机自动生产线适合于小件及简单件的成型。
双臂步进梁电动螺旋压力机自动生产线
参展单位:榎本机工株式会社
展位号:W2-W88
展品型号和名称:伺服马达螺旋压力机
技术参数
50%节能、不需保养、高精度
由伺服马达直接驱动的螺旋压力机。
完成一个工作循环时,机械制动不会启动由伺服马达停止滑块。此时伺服电机发电回生电力。机器不使用压缩空气,综合减少约50%电力消耗。制动垫片可以永久使用不用更换,没有离合器垫片。
几乎不需要保养,成型能量每次相同不会变动,全自动且24小时生产时,有5年以上没有故障停止的事例。
参展单位:上海舒勒压力机有限公司
展位号:W2-V38
展品型号和名称:PZS900f型电动螺旋压力机
技术参数:中心载荷时容许的持续压力128 000 kN
冷击力10%行程次数之内160 000 kN
行程约为900mm时的总工作能量3 150 kNm
螺杆直径900 mm
滑块最大行程900 mm
滑块最小行程500 mm
舒勒拥有近120年螺旋压力机生产制造的经验,以及持续不断的研发,实际上几乎没有不能用螺旋压力机锻造的锻件。早在1936年,摩擦辊驱动就已取代了传统的摩擦驱动,随后又改为直接驱动。从1963年起,当可靠的三相同步电机(允许快速频繁启动)投入使用时,便打开了通向新的、理想的螺旋压力机驱动系统的大门。在直接驱动装置中,驱动电机的扭矩直接传递螺杆,没有中间传动部件、易损件或能量损失。从坚固性、可靠性,维修和效率方面来说,这种驱动装置代表了螺旋压力机驱动装置的最佳设计方案。
效率高,使用成本低
具有很高的锻造力
驱动系统无易损件
每次行程可使用100%能量
行程频率高
能量重复精度高
滑块行程停歇期间无动力消耗
能量可精确预置
维修、维护简单
设备简单、可靠,开机率高
能量从5%-100%之间可无级调节
参展单位:德国拉斯科成形技术有限公司(LASCO)
展品型号和名称:SPR 2000电动螺旋压力机
LASCO公司主要制造中等规格(4000吨)以下的电动螺旋压力机,主要用于航空、汽车、手术器械等精密锻件的生产;是世界上第一家将变频技术用于电动螺旋压力机驱动系统的公司。
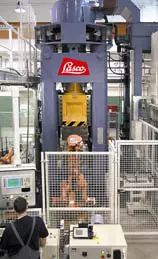
与老式的摩擦驱动方式相比,拉斯科的直接电驱动方式具有可靠性好、经久耐用和磨损较少的明显优势。一般来讲,当压力机的公称压力小于6300KN时,通常使用传统的异步电机来驱动,但是对于更大规格的压力机,必须配备一个具有无功电流补偿功能的变频器,可以大大改善机器的技术性能,并且功率因数可提高3倍。
电机驱动螺杆反时针方向旋转,螺杆与螺母相配合驱动滑块向下运动。在行程结束点,电机反转,带动滑块回到初始位置(上死点)。
要想在额定滑块行程上获得额定能量,滑块必须加速。通过将速度和位置数据反馈到PLC中,模具就能获得预想的打击速度。
如果要得到较小的能量,电机加速到一个理想的位置,然后让滑块减速,并在打击工件时获得所要求的速度。由于采用这种驱动方式,即使在公称行程下,都能保证在最短的时间内获得任何所需要的能量。
它还可以在保持设定能量的前提下,将公称行程提高到所需要的任何数值。
在很小的公称行程时也可以工作,但是要减小公称能量。最大的计算能量在屏幕上有显示。
当完成工作行程后,电机驱动滑块加速回程,停在计算好的位置,准备下一次打击。
滑块在上升和下降过程中被制动的时候,电机就变成了发电机。有机械能产生的电能将输回电网。
在所有的运行阶段,变频器几乎都不会产生无功电流。
拉斯科变频驱动系统的优势:
最佳的工艺稳定性,源自最佳的打击能量和打击力的重复精度(精确的能量测定)。
在小能量打击时可获得更快的生产节拍。
通过降低电源的峰值载荷,大大降低对主电源的苛刻要求
由于对供电要求很低,所以减少了电源电缆的截面积(即电源电缆直径变小)
避免了机械制动造成的维修成本
高效率,大大节省了电力成本
感应加热炉
参展单位:应达集团中国
展位号:W2-X25
展品型号和名称:Uniforge一体式锻造中频感应加热炉
技术参数
设备功率:50kw~1000kw,额定频率:500hz~30khz
1.进出料机构、线圈、内部闭式水冷系统、电源及控制系统等一体化设计,结构紧凑牢固
2.可以在任何温度、任何负载情况下快速100%启动成功;
3.国际领先的串联谐振式电源技术,全波二极管整流,能量转换效率达95%以上;
4.可控输出功率范围10~100%,且在任何负载下电源功率因数都可以达0.92以上;
5.谐波污染少,无需额外消谐装置即可满足国家电网关于谐波的标准要求;
6.一体化设计,铜排距离短;串联电源逆变侧高电压,低电流;任意负载下的高功率因数等各种优点,使得中频的能耗较低;
7.先进的三维模拟软件用于设计坯料在线圈中的加热温度曲线,温度控制精度高,稳定性好;
8.电源及控制系统关键元器件采用进口件以及国内外知名品牌部件,世界领先的技术,本地化的服务和价格;
9.丰富的自检测、诊断及报警功能和多重安全防护装置。
10.可选配全自动步进式上料机系统。该系统结构紧凑,适应坯料直径宽,上料稳定,可满足自动生产线等的生产需要。
参展单位:重庆恒锐机电有限公司
展位号:W2-R30
展品型号和名称:5600KW中频感应加热炉
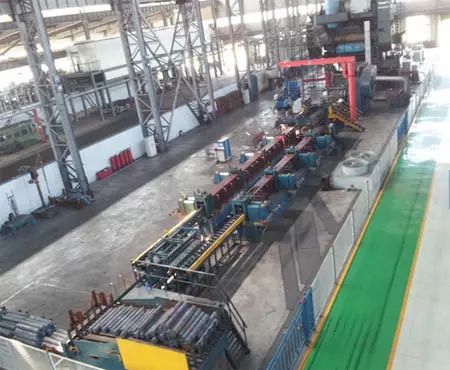
配套压力机为俄罗斯14000T热模锻压力机;国产最大功率中频加热炉;全自动化传输。
参展单位:山东荣泰感应科技有限公司
展位号:W2-W26
展品型号和名称:GT2000KW×2双线自动锻造加热炉
技术参数
额定功率:2000KW×2
额定输入电压:六相660V 50Hz
额定产能:9.75T/小时
额定加热温度:1250摄氏度
加热坯料规格:Φ80-Φ240
1、双线布置,交替送料;
2、配阶梯自动上料装置;
3、连续夹棍送料,速度自动连续可调;
4、成套设备计算机自动控制加热,合格的坯料自动输送到指定位置并发出信号,由机器人抓取到后道工序。
自动化装备及生产线联线
参展单位:潍坊西水机器人科技有限公司
展位号:W2-V30
展品型号和名称:步进式机器人
步进式机器人不仅具备了六轴工业机器人的优点,还凝聚了步进梁的特点。
步进式机器人的优势在于:
1)灵活,重复定位精度高;
2)实用性强,可适应不同规格不同种类产品的生产;
3)效率高,节拍快;
4)操作简单,更换产品时只需更换齿爪即可;
5)故障率低,寿命长;
6)维修方便,压力机检修时,不需拆卸模架;
参展单位:AGANG TECH CO., LTD.
展位号:W2-Q44
展品型号和名称:Forging Press Automation Line
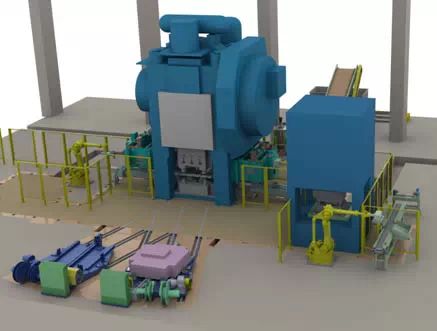
安装在各种冲压机上,使冲压加工更迅速,实现冲压工艺的自动化,与其他方式的TRANSFER FEEDER相比,工艺控制效率更高,大幅度提高生产效率。本设备可以用于包括冷、温、热等任何形式的冲压加工方式。
锻造工序上的脱离剂的喷射是保证产品的质量和延长模具寿命的非常重要部分。
通过伺服器控制脱离剂喷射系统,保证脱离剂的涂喷更精确和与SERVO TRANSFER FEDDER的联动,缩短加工时间和通过精确的脱离剂涂喷延长模具的寿命。
本设备是调整微合金化钢的锻造中冷却速度,节省锻造工序后热处理工序的设备,缩短热处理需要的时间和节省费用。
本设备是用来快速、安全地拆换冲压机的模具的设备,设计和制造时充分考虑到冲压机和模具的特点。
参展单位:北京机电研究所
展位号:W2-R38
展品型号和名称:12500T曲轴锻造生产线自动化装备及生产线系统
生产线模拟,自动化总线控制系统,9台机器人,2个缓冲存料机构,3台固定存料机构,3个抽检传送装置,4个中转料台,安全雷达,安全围栏,安全光栅,主机/切边视觉系统等物料传送及检测设备。
该生产线设计充分吸收了蒂森克虏伯德国,美国及巴西曲轴锻造生产线的优缺点,结合北京机电研究所几十年来在锻造生产线上积累的丰富经验,生产效率,自动化程度,设备可靠性,安全标准等有很大提升,代表了我国自主研发的锻造自动生产线的最高水平。整条锻造生产线从钢棒料放入锯床上料机构开始,锯切下料,加热,辊锻,预锻,终锻,切边,整形,冷却,整个过程全部由机器人或传送装置自动完成。整条生产线共分为6个控制区域,所有生产过程均通过自动化总线控制系统进行实时监控,尤其是视觉识别系统在预锻、终锻、切边等几个位置的自动检测大幅度提高了自动生产过程的稳定性、可靠性,大幅提高了出现问题后快速处理的反应时间。整条锻造生产线在生产过程中完全封闭,能够做到出现问题后根据自动化程序设定自动处理,实现无人为干预。
参展单位:意大利菲赛普(FICEP)公司
展位号:W2-V33
展品型号和名称:机器人及自动化生产系统
菲赛普公司在自动化锻造系统的开发和应用上有着丰富的经验,经典案例包括汽车半轴自动化生产线、石油钻杆接头生产线、复合锅底生产线等。菲赛普根据不同的产品规格和产量要求配置生产线,典型的半轴自动化生产线由以下部分组成:
下料(棒料冷剪机或圆盘锯)
感应加热+液压机多级模锻
电热镦粗+螺旋压力机锻造
生产线全面采用机器人自动化物流系统,满足用户优质、高效、节能、环保要求,并营造人性化的生产环境。
参展单位:德国拉斯科成形技术有限公司(LASCO)
展品型号和名称:HO-U 500电液模锻锤全自动化汽车连杆锻造生产线
技术参数
工艺流程:上料(震动给料机)-加热(感应加热炉)–制坯(楔横轧机)–模锻(压扁、预锻和终锻)(电液模锻锤)-切边(机械压力机)–冲孔(机械压力机)–热校正(机械压力机)-称重–冷却。
其中另含:锻造机器人2台,下料机械手1台,切边机器人2台,飞边移除装置1套,传送带3条,自动称重装置1套。
锻件毛坯最大单件重量为1.2Kg,重量公差:±1mm,锻件厚度公差:0.2mm。
生产纲领:500万支/年。每天领班每班8小时,每周6天,全年工作日313天。年小时基数为5000小时,设备负荷率80%.。
该生产线是目前国内外最先进的电液模锻锤全自动化汽车连杆锻造生产线,已在国内外投产使用近二十条,其中一条于2009年安装在云南西仪工业股份有限公司。
锻锤生产线在环境方面比锻造压力机更具有优势,锻造不需要任何冷却和润滑,模具与锻造压力机相比也更简单。在世界上,大部分连杆是采用锻锤锻造而成的,此外,采用锻锤生产的锻件质量更高,锻件的厚度公差可以保持在±0.05mm的范围。模具寿面也是锻锤的显著优势之一,在理想状态下,一套模具可以生产10万件连杆。锻造压力机的维护、离合器和制动器的使用寿命等总带来一些问题,锻锤则非常简单、精确、耐用。
锻造机器人采用LASCO特殊设计,配有专利夹钳。
|